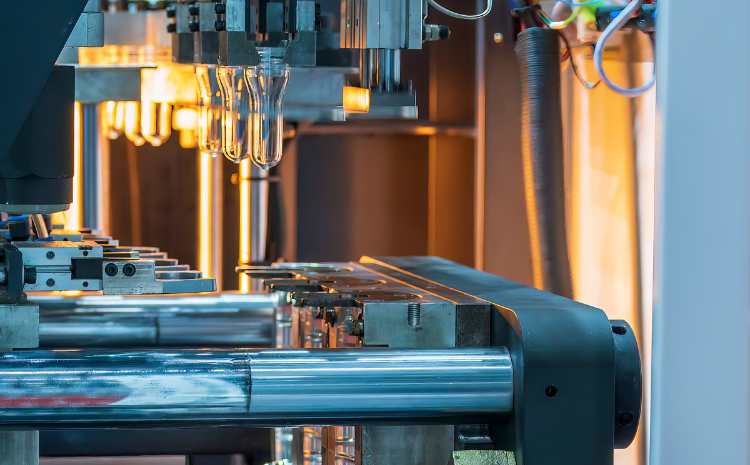
The Role of Fully Automatic Shrink Wrapping Machines in Product Protection
Introduction
Product safety and longevity remain top priorities within today’s rapidly evolving manufacturing and packaging industry. The fully automatic shrink wrapping machine stands out as one of the best solutions for reaching this goal. Shrink wrap machines enable seamless product wrapping while providing efficient protection with shrink film against external threats. The shrink wrapping machine proves to be a revolutionary packaging solution as companies search for dependable methods to protect products throughout storage and shipping.
Shrink wrapping technology has become highly popular across multiple sectors including food and beverage as well as pharmaceutical and electronic industries. This process delivers effective protection for products against environmental risks and physical damage while preventing tampering. Globally businesses have embraced automatic shrink wrap machines for water bottle shrink wrapping as well as plastic wrapping machines which includes shrink tunnel wrapping machines because they deliver improved product safety and operational efficiency.
A Fully Automatic Shrink Wrapping Machine represents an advanced packaging system designed to automate and optimize the shrink wrapping procedure.
A high-performance packaging system called a fully automatic shrink wrapping machine functions to automate and streamline the shrink wrapping process. The machine securely encloses products within shrink film and uses heat to develop tamper-proof and protective packaging. These machines optimize operations by decreasing human intervention during tasks while simultaneously boosting the rate of packaging and maintaining high-quality standards.
Several industries including food production, beverage manufacturing, pharmaceuticals, electronics, and consumer goods utilize shrink wrapping technology extensively. When heated the shrink film wraps products tightly to provide protection from dust, moisture, and bacteria and boosts their shelf appeal. Fully automatic shrink wrapping machines operate with minimal human input which makes them perfect for large-scale production settings unlike their semi-automatic counterparts.
The machines include multiple advanced parts such as heat shrink wrappers together with shrink tunnel machines and systems for automated film feeding and cutting. The shrink tunnel machine uses carefully regulated heat to achieve consistent shrinkage of the wrapped product without damaging it. These machines accommodate different product dimensions and packaging needs efficiently through their adjustable temperature settings and conveyor speed controls.
Main Attributes of Complete Automatic Shrink Wrapping Equipment
- Fully automatic shrink wrappers are capable of handling hundreds to thousands of products each hour which significantly boosts productivity for high-demand industrial applications.
- Operators need minimal manual adjustments when operating machines compared to traditional shrink wrappers which necessitate full human control.
- These machines offer flexible packaging solutions for several products including bottled beverages and food trays as well as pharmaceutical kits and electronic components.
- Shrink wrapping provides tamper-proof packaging which protects products against contamination and physical damage while preventing unauthorized access.
- Heat shrink wrappers produce a clear and smooth finish that is wrinkle-free which enhances how products look.
- The majority of fully automatic shrink wrapping machines enable effortless integration with conveyor systems and other packaging equipment to create a fully automated packaging workflow.
The increasing need for efficiency and accuracy in packaging operations has made fully automatic shrink wrapping machines a critical component of contemporary manufacturing systems. Businesses choose these machines because they deliver reliable, fast packaging solutions that are also cost-effective to improve production capabilities.
This chapter details how shrink wrapping machines function.
A shrink wrapping machine functions through a sequence of synchronized operations which guarantee secure packaging of products with protective shrink film. Industries that prioritize packaging quality alongside product safety and operational efficiency depend heavily on this process. The subsequent text provides a detailed explanation of the functioning process of an automatic shrink wrap machine.
- Product Placement
The shrink wrapping process starts when products enter the machine by being placed on a conveyor belt or in the loading area. Semi-automatic shrink wrapping machines require manual product placement while fully automatic machines perform this task automatically. The conveyor belt transports products into the wrapping section where they enter a seamless packaging process.
Automated product placement reduces manual handling requirements while promoting consistent packaging results for high-volume production industries including food, beverages and pharmaceuticals. Multiple bottles are arranged in groups during water bottle shrink wrapping before they proceed to the subsequent stage.
- Film Enclosure
When the product arrives at the wrapping station shrink film made from materials such as polyethylene, polyolefin, or PVC gets unrolled and goes around the product. The shrink film either fully encloses the product or creates specific open areas which shrink to form a secure seal according to packaging requirements.
Certain shrink wrap packaging machines apply single-wound film whereas others make use of center-folded film to wrap products effectively. The selection of shrink film requires consideration of both the required protection level and the specific product characteristics. Specialized shrink wrap films with superior durability and transparency protect fragile or perishable products to preserve their integrity.
- Sealing the Film
After wrapping the product with the film it must be sealed to create a protective enclosure. The shrink wrap sealer machine or shrink wrap bottle sealer becomes important at this stage. The sealing mechanism combines heat with pressure to bond film edges together creating a secure wrap.
Automated sealing systems enable rapid processing without requiring human control. The effectiveness and visual quality of packaging depend on sealing performance which requires precise sealing parts to prevent incomplete or loose wraps.
- Heat Shrinking Process
Once the film is sealed onto the product it enters the shrink tunnel machine where heat forces the film to contract around the item. When exposed to heat the film undergoes contraction which allows it to snugly fit the contours of the product.
Heat shrink packaging machines maintain precise temperature control and airflow while adjusting conveyor speed to ensure proper shrinkage without damaging the product or film integrity. Certain shrink tunnels use infrared heaters to create heat while others depend on hot air circulation for uniform temperature distribution.
Automated shrink wrappers help high-speed packaging industries achieve efficient shrink wrapping processes while protecting products. The shrink tunnel stage plays a crucial role in plastic wrapping machines by producing both professional appearance and tamper-resistant packaging.
- Cooling and Final Packaging
After the heat-shrinking operation ends the wrapped item leaves the shrink tunnel machine to move into the cooling section. The cooling area uses fans or ambient air to let the film harden against the product for a tight and secure packaging solution.
The cooling process protects packaging from warping or distortion. Before distribution products may receive extra labeling or secondary packaging in certain scenarios.
At process completion, the product features a secure wrap that looks attractive and shields against moisture and dust while preventing tampering. The automated shrink wrapping process improves efficiency and packaging quality while minimizing human error which makes automatic shrink wrap machines essential for high-production environments.
Fully automatic shrink wrapping machines provide numerous advantages including boosted efficiency and improved packaging consistency while minimizing human mistakes.
Enhanced Product Protection
Shrink wrapping provides dependable protection from moisture, dust and contaminants which makes it the perfect packaging option for various products. Perishable products like food and pharmaceuticals require packaging solutions that preserve their integrity which makes this packaging type highly beneficial. Shrink wrap packaging machines use heat to activate specialized shrink film around the product which creates a tight seal that blocks air and bacteria while also protecting against environmental pollutants. Electronics manufacturers rely on shrink wrapping to safeguard delicate components against static electricity, dust build-up and moisture while minimizing damage risks during storage and transportation. Shrink wrapping with secure tamper-evident seals gives customers confidence in the integrity of their products by showing that they remain unaltered throughout transit.
Improved Efficiency and Productivity
Small businesses could find manual and semi-automatic shrink wrapping methods effective but large-scale operations may find them too demanding because they require substantial time and manpower. The efficiency of fully automatic shrink wrapping machines increases dramatically since they process hundreds or thousands of products every hour based on machine capacity. Industries such as bottled beverages, pharmaceuticals, and consumer goods benefit from this high-speed packaging capability because they require rapid wrapping and distribution of large product volumes. Automated shrink wrapping decreases manual labor needs while maintaining uniform packaging standards. Implementing fully automatic shrink wrappers allows businesses to achieve more efficient production lines while reducing human errors and boosting productivity.
Cost-Effectiveness
The long-term financial benefits of investing in shrink wrapping machines become substantial. The implementation of automation limits the need for intensive manual labor which subsequently reduces operational costs. Shrink wrapping machines ensure material conservation by reducing waste more effectively than traditional packaging approaches. The cost of shrink wrapping machines depends on their features and production abilities but companies regularly see a substantial return on investment because they achieve better efficiency and packaging accuracy alongside shorter downtime intervals. Shrink wrapping machines enable businesses to produce high-quality packaging solutions while reducing material waste and labor expenses and maximizing production output.
Customization and Versatility
Shrink wrapping technology stands out because it can adjust to diverse product dimensions, configurations, and materials. Automatic shrink wrapping machines can handle diverse packaging needs including small consumer goods, large industrial equipment and delicate pharmaceutical products. Businesses can choose their ideal packaging material because these machines work with multiple film types such as PVC, polyolefin, and polyethylene. A range of industries utilize bottle shrink wrappers and plastic wrapping machines alongside shrink tunnel wrapping machines to provide businesses with customizable packaging solutions for different products. Product protection reaches its peak when businesses utilize adjustable film thickness and wrapping methods which also preserve a professional product look.
Enhanced Aesthetic Appeal
The way products are displayed makes a big difference in how they catch consumer attention and sway buying choices. Shrink-wrapped products display a sleek and polished appearance which provides them with a professional aesthetic that boosts their attractiveness on retail shelves. Heat shrink machines create a smooth and clear protective wrap around products resulting in a perfectly sealed package free from wrinkles. The use of this packaging technique benefits consumer goods as well as electronics and retail products because it creates an aesthetically pleasing appearance which helps brands differentiate themselves. Businesses have two packaging options, shrink wrap tunnels for sale and heat shrink wrap machines, which deliver high-quality protection and improved marketability for their products. Companies find shrink wrapping appealing because it enables straightforward labeling and branding which improves product presentation.
Shrink wrapping enables businesses to protect products better while improving efficiency and reducing costs while creating attractive packaging suitable for numerous industries.
Applications of Shrink Wrapping Machines
Food and Beverage Industry
Shrink wrapping serves as an essential packaging solution for the food and beverage industry by providing secure packaging that preserves product freshness. The shrink wrapping method is commonly employed for packaging bottled beverages along with processed foods, dairy items, and perishable products. The common application of shrink wrap for water bottles involves bundling multiple bottles together to optimize transportation and storage efficiency. The food industry benefits from heat shrink packaging machines because their airtight seal keeps food products protected against contamination and moisture along with external elements. Shrink-wrapped food items retain their attractive appearance on retail displays which draws consumers’ attention while at the same time ensuring prolonged shelf life. Food manufacturers use automated shrink wrapping machines to adhere to hygiene and safety regulations through producing uniform and secure packaging.
Pharmaceuticals
The pharmaceutical industry requires packaging solutions that deliver exceptional precision and safety to prevent contamination and tampering while shielding products from humidity and light. Bottles together with blister packs and medical kits benefit from shrink wrap packaging which stands as the optimal method for safeguarding medicine and healthcare product integrity. Automated shrink wrap machines serve as essential tools in pharmaceutical production lines to seal medicine bottles, syringes, bandages and diagnostic kits efficiently. Shrink wrapping produces an airtight seal and provides tamper-evidence which maintains product effectiveness while deterring counterfeit products and lengthening shelf life. Pharmaceutical companies frequently choose shrink tunnel packaging machines with advanced heat control capabilities to protect sensitive medications throughout the packaging process.
Electronics
The high sensitivity of electronic devices and components to dust, moisture, and static electricity requires protective packaging to prevent damage. The electronics industry frequently employs shrink tunnel packaging machines to package products including mobile phones along with chargers, batteries, computer accessories and circuit boards. The shrink film delivers strong protection through a clear layer that maintains product safety while minimizing additional weight and volume. Shrink wrapping functions as a tamper-proof packaging solution that ensures customers receive brand new and untouched products. Anti-static properties in some shrink wrap films help shield delicate electronic components from static electricity accumulation throughout transportation and storage.
Retail and Consumer Goods
In retail environments product presentation along with security measures serve as essential elements that affect customer buying choices. Shrink wrapping machines serve as an effective packaging method for a wide range of consumer products including cosmetics, personal care items, household essentials and luxury merchandise. A multitude of businesses apply heat shrink tunnel machines to give their products professional and polished styling which boosts brand value while attracting consumers. The retail industry benefits from shrink wrapping because it provides tamper-proof packaging that protects products from unauthorized access and maintains their intact condition upon delivery. Retail distribution benefits from shrink-wrapped products due to their easy handling and storage capabilities.
Choosing the Right Shrink Wrapping Machine
Businesses that require efficient and high-quality packaging must carefully choose their shrink wrapping machine. Businesses need to assess multiple factors to select a shrink wrapping machine that fulfills production needs and stays within budget while being compatible with packaging materials. The right shrink wrap system investment leads to better product protection and more efficient packaging operations.
Production Volume
Businesses need to select shrink wrapping machines based on their production scale requirements. Businesses that need to process large product quantities should choose fully automatic shrink wrapping machines because they provide quick and efficient packaging solutions. Industries like food and beverage and pharmaceuticals require shrink wrapping machines because they deliver quick and consistent packaging results. Small or medium-sized businesses that produce lower volumes can choose semi-automatic or manual shrink wrap machines to fulfill their packaging requirements without exceeding their budgets.
Film Type
Each product needs a specific shrink film type to achieve both proper sealing and protection. The selection of appropriate shrink film plays a critical role in preserving the packaging’s integrity. A variety of films including PVC (Polyvinyl Chloride), Polyolefin and Polyethylene can be used with heat shrink wrap machines. Polyvinyl Chloride (PVC) serves as the material of choice for lightweight products while Polyolefin stands as the preferred option for food packaging because of its excellent clarity and robustness. Products with heavy weight or unusual shapes benefit from the tough nature of Polyethylene films for bundling purposes. The compatibility of shrink film with the machine ensures both packaging security and visual appeal.
Budget
The cost of shrink wrapping machines changes depending on their automation technology and production capabilities as well as their supplementary features. Companies need to evaluate various models and manufacturers to select a cost-effective option within their financial limits. Despite their higher upfront costs, fully automatic machines save money over time because they minimize labor expenses and boost productivity levels. Small-scale operations find semi-automatic machines to be more economical while manual shrink wrappers remain the most cost-effective solution for companies with basic packaging requirements. Analyzing the full ownership costs alongside maintenance and film expenses plays an essential role in the purchasing decision process.
Machine Features
The latest shrink wrapping machines offer multiple sophisticated features which boost both packaging quality and efficiency. Automation capabilities, sealing efficiency and heat distribution stand out as the essential features to examine when choosing a shrink wrapping machine. The use of fully automatic machines reduces human involvement while simultaneously decreasing packaging mistakes and improving packaging uniformity. Well-designed sealing systems offer secure packaging solutions that protect products from tampering and damage during shipping. Achieving a uniform shrink wrap without any wrinkles or burns requires an even distribution of heat throughout the packaging process. Touchscreen controls combined with adjustable settings and safety mechanisms create simple operation while boosting overall machine performance.
Businesses can achieve their specific operational requirements through the dependable manufacturing of shrink tunnel machines by a trustworthy producer. Investing in the proper equipment leads to better product quality while minimizing waste and speeding up packaging operations which makes it essential for any company.
Innovations in Shrink Wrapping Technology
Technological innovations continue to enhance the performance of shrink wrapping machines by increasing their efficiency and sustainability while improving reliability within the packaging sector. Manufacturers are adding new features to their products that improve performance and energy efficiency while they respond to growing demands for eco-friendly packaging solutions.
Energy-Efficient Heat Shrink Tunnels
Businesses aiming to reduce operating expenses need to prioritize energy consumption. Modern shrink wrapping machines feature energy-efficient heat shrink tunnels which lower power usage without sacrificing performance quality. Such systems incorporate advanced heating technologies and enhanced insulation to reduce thermal loss which enables accurate temperature regulation. The optimization of energy consumption enables businesses to achieve lower electricity expenses and simultaneously diminish their environmental footprint.
Eco-Friendly Shrink Wrap Materials
The push towards sustainability defines today’s packaging solutions while shrink wrapping technology adjusts to fulfill these modern requirements. Shrink film manufacturers produce eco-friendly packaging options from biodegradable materials that support recycling efforts. The materials work to minimize plastic waste while keeping traditional shrink wrap’s protective and visual features intact. Sustainable-focused businesses have the option to select shrink wrap films which are compostable or recyclable and meet global environmental standards. Specific shrink wrap machines operate with thinner films while maintaining structural integrity to minimize material waste.
Smart Automation and IoT Integration
The emergence of Industry 4.0 has led to the transformation of shrink wrapping technology through smart automation and Internet of Things (IoT) integration. The latest shrink wrap machines contain sensors and data analytics functions which facilitate real-time machine monitoring along with the ability to operate remotely and perform predictive maintenance. Businesses can monitor machine operations while identifying potential problems ahead of time and improving packaging processes through these intelligent capabilities. IoT-enabled machines can be connected to different production systems to establish a seamless automated workflow which increases overall productivity.
Enhanced Sealing and Cutting Mechanisms
High-quality shrink wrapping depends on precise sealing and cutting methods. Recent developments in sealing technology have produced sealing mechanisms that deliver improved efficiency and longevity while enhancing package integrity. Through uniform heat distribution advanced sealing systems produce durable airtight seals that guard against contamination and damage. Modern shrink wrap machines incorporate advanced cutting mechanisms which deliver seamless and accurate cuts without producing jagged edges. The enhanced features of shrink-wrapped products improve both their visual appeal and functional performance which leads to increased consumer interest.
Businesses can achieve better packaging efficiency and lower expenses while supporting environmental sustainability through the adoption of new technologies. Shrink wrapping technology advancements are enhancing product protection while simultaneously changing the packaging industry to address current requirements.
Conclusion
The complete automation of shrink wrapping machines represents an essential business tool for organizations aiming to increase product protection while optimizing packaging operations. Shrink wrapping serves as an economical and attractive packaging method that ensures product protection across various industries including food, beverages, pharmaceuticals, and electronics. Investing in an appropriate shrink wrapping system allows businesses to enhance operational efficiency while saving costs and providing consumers with premium packaged products.
Technological improvements in heat shrink machines alongside plastic wrapping machines and shrink tunnel packaging machines enable companies to protect their products for extended periods and maintain product safety. Selecting a proper shrink packaging machine manufacturer allows businesses to maintain market leadership and adhere to superior packaging standards.