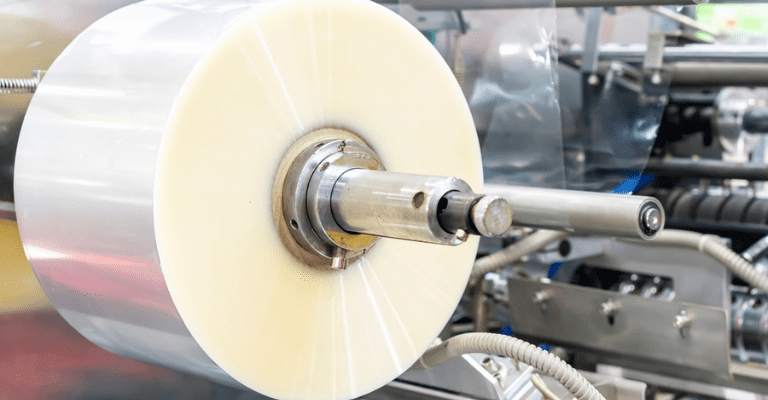
Introduction to Shrink Packaging
Definition and Overview
Shrink packaging, a cornerstone in the realm of packaging technology, involves using polymer plastic film to wrap products, after which heat is applied to the covered material, causing the film to shrink tightly. This technique is indispensable across industries, offering protection while maintaining product integrity, providing tamper evidence, and even enhancing aesthetic appeal for retail advantage.
Historical Background of Shrink Packaging Technology
The journey of shrink packaging technology dates back to the mid-20th century, evolving with the introduction of polymer science. Early methods were rudimentary, often inconsistent in application and heat control. However, the ensuing decades witnessed significant advancements in material science and automation technology, propelling shrink packaging into a new era characterized by efficiency, reliability, and adaptability to various product forms.
- The Science of Shrink Packaging
Understanding Polymer Films: Composition and Type:
At the heart of shrink packaging is the polymer film, predominantly composed of materials like Polyethylene (PE), Polyvinyl Chloride (PVC), and Polyolefin. Each material possesses unique characteristics impacting strength, clarity, shrink ratio, and application suitability. For instance, Polyolefin is preferred for its versatility and FDA-compliance for food contact, while PVC is prized for its strength and rigidity.
The Shrinkage Process: How Heat Transforms the Film
The pivotal moment in shrink packaging is the application of heat. As the polymer film heats up, it reaches a point of plastic deformation, changing physically without losing integrity. This process is a delicate balance; excessive heat can cause the film to break, while insufficient heat won’t provide the necessary shrinkage. Modern machines are adept at maintaining this balance, ensuring uniform heat application for consistent results.
Environmental and Physical Properties of Shrink Films
The environmental and physical properties of shrink films are critical to their performance. Their puncture resistance, clarity, printability, and seal strength come into play during packaging and logistics. Moreover, the films’ behavior in different environmental conditions, including their reactivity to temperature fluctuations and sensitivity to UV light, determines their suitability for various products and storage conditions.
III. Core Components of Shrink Packaging Machines
Unwinding Unit: Managing Film Rolls
The initial phase in the machinery involves the unwinding unit, where rolls of shrink film are systematically unwound. This unit is integral in preventing film tangles or tears, ensuring a smooth transition into subsequent stages.
Sealing and Cutting Assembly: Precision in Packaging
Here, precision is key. The film wraps around the product, after which the sealing and cutting assembly melts its edges, creating a seal before cutting off the excess. Modern machines employ a hot knife system, preferred for speed and efficiency, and ensuring the film doesn’t stick to the product.
Heat Tunnel: The Heart of Shrink Transformation
The heat tunnel is the core of the transformation process, where wrapped products undergo controlled heat exposure, causing the film to shrink. Advanced machines maintain consistent temperature, ensuring uniform shrinkage and quality finish, irrespective of product shape or size.
Outfeed System: Handling Packaged Products
Post the heat tunnel, the outfeed system manages the flow of products, now tightly encased in shrink film. This component is vital for organizing the output, preventing damage, and sometimes cooling the products before they’re further processed or palletized.
Control Panel: Command Center for Operations
The control panel is the operational brain of the machine, housing the user interface for managing all machine settings. It offers control over temperature, conveyor speed, and sealing time, among other parameters. Sophisticated models provide advanced diagnostics, alert systems, and programmable settings for different products.
- Categories of Shrink Packaging Machines
L-Sealer Machines
L-Sealers are fundamental to shrink packaging, responsible for sealing the film around a product. They are prized for their ability to handle a wide range of product sizes, aided by their ‘L’ shaped sealer bar, and are compatible with various film types.
I-Bar Sealers
I-Bar sealers are simplistic yet effective, often used for low-volume applications. They utilize a single bar to seal films, making them ideal for products requiring manual handling, offering flexibility, and ease of operation.
Shrink Tunnels
A shrink tunnel is a dedicated chamber where the heat-induced shrinkage occurs. These machines vary in size and heating methods, catering to diverse operational scales and product types. Their proficiency determines the quality of the shrink packaging finish.
Automatic Shrink Wrap Systems
These are the epitome of efficiency, combining sealing and shrinking into a single operation. Automatic systems significantly increase production speed, reduce labor costs, and are ideal for high-volume packaging needs. They minimize human intervention, ensuring consistency and quality throughout the packaging process.
Sleeve Wrappers
Sleeve wrappers, specifically designed for bulkier items, use two rolls of film to create a sleeve around a product, after which the product passes through a shrink tunnel. They are prominent in industries requiring bulk packaging solutions,
- Operational Mechanics of Shrink Packaging Machines
Step-by-Step Process Description:
The operational mechanics begin with the preparation of the shrink film, typically wound on a roll, which is then fed into the machine. The product to be packaged is placed on the conveyor belt and transported into the machine, where the film wraps around it. The machine’s sealing cutter then envelops the product by trimming and sealing the film, forming a bag around the item.
As the product progresses, it enters the heat tunnel. This critical phase involves circulating hot air around the film, causing it to shrink and mold itself to the product’s contours. After shrinking, the package is often subjected to a cooling phase, solidifying the film’s fit and finish around the product, ensuring a tight, secure, and aesthetically pleasing result.
Role of Automation in Shrink Packaging:
Modern shrink packaging machines are increasingly automated, combining technology and convenience to streamline operations. Sensors detect products as they enter the machine, adjusting the settings automatically based on pre-programmed criteria. These automated systems are particularly beneficial for high-volume packaging needs, offering consistent quality, reducing manual labor, and minimizing errors or defects in the packaging process.
Human Interface and Operational Safety Measures:
While automation plays a key role, human interaction with these machines is still essential. Modern interfaces are user-friendly, often featuring touch screens and easy-to-navigate menus. Safety is also a paramount concern. Features such as emergency stop buttons, automatic shut-offs if a safety door is opened, and clear safety instructions are standard. Regular training ensures staff understand how to operate the machines safely and efficiently.
- Technical Innovations in Shrink Packaging Machines
Digitalization and Smart Controls:
Today’s shrink packaging machines are integrated with digital controls and smart systems that ensure precision, efficiency, and connectivity. Programmable Logic Controllers (PLCs) are commonly used for greater control over machine functions, from temperature regulation to conveyor speed. These digital enhancements contribute to quality assurance, repeatability, and minimal downtime.
Energy Efficiency Practices:
Energy consumption is a significant consideration in machine operation. Recent advancements focus on reducing this aspect through improved heat tunnels that require less power, newer models of sealers with energy-efficient operations, and overall machine designs that contribute to lower energy use without compromising performance.
Use of Advanced Materials and Components:
Components used in these machines must withstand high temperatures and stress. Advanced materials, such as higher-grade metals, heat-resistant plastics, and durable composites, are integral to modern designs. These innovations contribute to a machine’s longevity, reliability, and ability to perform at optimal levels consistently.
Safety and Maintenance Innovations:
Maintaining these machines is streamlined through innovative features like self-diagnostic capabilities, which notify operators of issues before they become critical problems. Safety enhancements, such as improved ventilation systems, reduce overheating risks, while routine maintenance reminders contribute to a holistic approach to operational safety.
VII. Customization and Versatility in Shrink Packaging
Accommodating Various Product Dimensions:
One of the most critical advancements in shrink packaging technology is the machines’ ability to accommodate various product sizes. This versatility is achieved through adjustable sealing arms, customizable conveyor belts, and settings that can be quickly reconfigured for different products. Such features ensure that businesses with diverse product lines do not need multiple machines.
Adaptability to Different Film Types:
Modern machines can work with a range of shrink film types, including PVC, polyolefin, and polyethylene, each offering different qualities and suitable for various applications. This adaptability is crucial for companies needing to switch between products with different packaging requirements.
Custom Features and Add-Ons for Specific Industries:
Many industries have unique requirements, and shrink packaging machines are increasingly designed with the flexibility to accommodate these. For example, the food industry might require a nitrogen-flush option to preserve freshness, while electronics manufacturers may need anti-static film compatibility. These customizations ensure that all industry needs are met with tailored solutions.
VIII. Industries Relying on Shrink Packaging Solutions
The application of shrink packaging transcends numerous industries, given its versatility and the protection it offers products.
- Food and Beverage: Critical in maintaining freshness, shrink packaging is vital here. It keeps contaminants out, often used in conjunction with modified atmosphere packaging to extend shelf life. Additionally, it offers tamper-evident solutions, ensuring consumer trust.
- Pharmaceuticals: The stakes for contamination and tampering are high. Shrink packaging aids in maintaining sterility and often provides a clear indication if a product has been tampered with, critical for consumer safety and regulatory compliance.
- Cosmetics: Beyond protection, the visual appeal is key in cosmetics. Shrink packaging allows for high-quality print finishes and special designs, enhancing shelf appeal. It also conforms to unique shapes, protecting individual components while showcasing them attractively.
- Electronics: Sensitive components require static protection, and anti-static shrink films are used widely. They protect from humidity, dust, and handling, ensuring the product reaches the consumer in working condition.
- Publishing: Books and magazines are prone to wear and tear, and shrink packaging protects these items during transit, often providing a resealable solution that consumers appreciate for long-term storage.
- Economic and Environmental Impacts of Shrink Packaging
Cost-Efficiency Analysis: Shrink packaging can be a cost-efficient solution. The materials are often less expensive than other packaging options, and the automation of the process allows for high volumes of product throughput. It minimizes packaging material waste, helping to keep costs down while maintaining product safety and appeal.
Sustainability Concerns and Eco-Friendly Adaptations: There’s a significant push for biodegradable and recyclable shrink films. The industry is responding with innovations like PLA (polylactic acid) films, which offer similar protective qualities while breaking down more easily in the environment. Companies are under increasing pressure to balance functionality and sustainability, making this a vital area of development.
Contribution to Supply Chain and Logistics: Shrink packaging consolidates products, making them easier to handle, store, and transport. This efficiency reduces costs in warehousing, transportation, and reduces the carbon footprint of these activities, contributing positively to supply chain optimization.
- Quality Control and Regulations
Monitoring and Maintaining Quality in Production: Consistency is the key to brand trust. This section would explore the systems in place for monitoring the quality of the packaging process, the standards that companies should adhere to, and how these are enforced in a production environment.
Compliance with International Standards and Certifications: With global trade, products need to meet international standards. These might include material safety data, machine safety standards, and environmental compliance. This compliance isn’t just bureaucratic but ensures the product’s acceptance in a global market.
Navigating Global Trade and Export Formalities: Companies need to be aware of the different regulatory environments they operate within. This section would cover how shrink packaging can help meet these requirements, from labeling and product information to ensuring the product arrives in a condition acceptable to the consumer.
Shrink packaging, a widely used method in the packaging industry, involves wrapping a product in a plastic film which is then subjected to heat. This process causes the film to shrink tightly over the item, offering protection and enhanced aesthetic appeal. This technology has revolutionized the way products are packaged, stored, and transported, making it a cornerstone in modern packaging solutions.
Basic Technology of Shrink Packaging
Shrink packaging utilizes materials such as Polyvinyl Chloride (PVC), Polyolefin, and Polyethylene, each offering distinct characteristics like clarity, shrink ratio, and strength. The process typically involves a sealer to cut the film around the product and a heat tunnel or gun to shrink the film. This method ensures the packaging is snug and secure, protecting the product from dust, moisture, and tampering.
Applications in Various Industries
Food and Beverage Industry
In the food and beverage sector, shrink packaging plays a critical role in preserving the quality and extending the shelf life of products. It is ideal for bundling products like water bottles, securing frozen foods, and packaging perishable items. This packaging method keeps products safe from contamination and aids in efficient transportation and attractive presentation in retail spaces.
Pharmaceuticals
For pharmaceuticals, shrink packaging ensures safety and compliance with health regulations. It offers a tamper-evident seal, crucial for medications, ensuring consumer safety. This packaging is also used for bundling products and promotional packaging, offering a versatile solution for the industry’s unique needs.
Consumer Goods
In the consumer goods sector, shrink packaging is employed for its versatility and aesthetic appeal. It’s widely used for electronics, toys, and other retail items, providing a clear view of the product while protecting it from damage and theft. This method also allows for creative branding and marketing, enhancing product visibility and appeal.
Environmental Impact and Sustainability
Environmental concerns have led to innovations in shrink packaging materials, making them more sustainable and recyclable. Biodegradable options and improved recycling processes are increasingly being adopted, addressing the environmental impact of plastic waste. These developments aim to balance the need for effective packaging with ecological responsibility.
Benefits of Shrink Packaging
Shrink packaging offers several advantages, including product protection, space efficiency, and cost-effectiveness. It provides a barrier against external elements, reduces storage and transportation costs due to its compact nature, and is adaptable to various product shapes and sizes. The clear packaging also enhances product visibility, aiding in marketing efforts.
- Challenges and Solutions in Modern Shrink Packaging
This section would provide an honest exploration of the current challenges facing the industry. From balancing energy consumption and production speed, addressing waste and sustainability concerns, to the need for skilled labor, each challenge would be met with current solutions and a look at what the future might hold. For example, innovations in materials science that offer improved recyclability, or advances in machine learning for better efficiency and automation, reducing the need for human intervention.
Despite its benefits, shrink packaging faces challenges like environmental concerns and the need for specialized equipment. Future developments focus on eco-friendly materials, automation in the shrink packaging process, and innovations to further enhance the efficiency and sustainability of this packaging method.
Shrink packaging, with its wide range of applications across various industries, plays a pivotal role in modern packaging solutions. Its ability to protect, preserve, and present products effectively, along with ongoing advancements, ensures its continued relevance and evolution in the packaging industry.