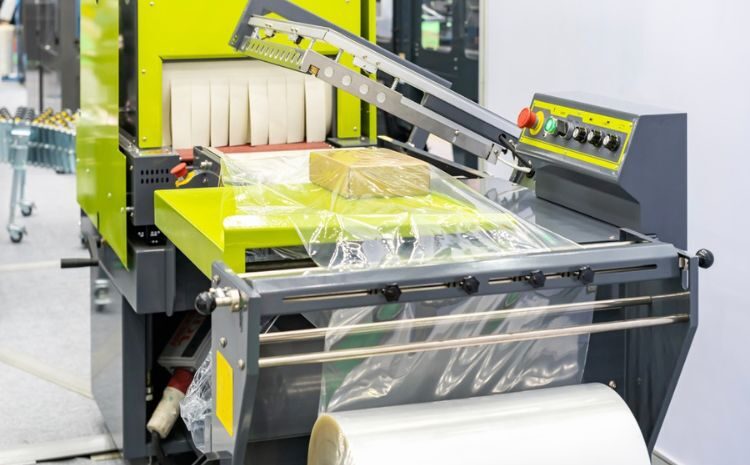
Choosing Shrink Wrapping Machines for Bottles: Key Factors
Choosing Shrink Wrapping Machines for Bottles: Key Factors
Shrink wrapping is an essential packaging solution for industries handling bottled products. Whether it’s water bottles, soda, or pharmaceuticals, shrink wrapping provides a secure, tamper-evident seal and enhances product presentation. Selecting the right shrink wrapping machine for bottles can significantly impact production efficiency, packaging quality, and operational costs. This guide delves into the critical factors to consider when choosing shrink wrapping machines, focusing on how they meet the demands of various industries.
Understanding Shrink Wrapping Machines for Bottles
Shrink wrapping machines are automated or semi-automated systems designed to wrap bottles in heat-sensitive film. When heated, this film contracts tightly around the bottles, ensuring a secure and professional seal. These machines are indispensable in industries such as beverages, food, and pharmaceuticals, offering both individual and grouped packaging solutions.
Key Benefits of Shrink Wrapping Machines
- Secure Packaging: Protects bottles during transit and storage, reducing the risk of spillage or contamination.
- Tamper-Evident Seal: Provides visible evidence if the packaging has been compromised.
- Aesthetic Appeal: Creates a polished look, improving shelf presence and brand visibility.
Types of Shrink Wrapping Machines for Bottles
Understanding the different types of shrink wrapping machines helps businesses select the most suitable option for their operations. These machines vary in terms of automation, speed, and capacity.
A.Manual Shrink Wrapping Machines
Manual machines require operators to load and seal bottles manually. They are ideal for small-scale businesses or those with limited production volumes. These machines are cost-effective but can be labor-intensive.
B.Semi-Automatic Shrink Wrapping Machines
Semi-automatic machines automate parts of the process, such as sealing and shrinking, while operators handle loading and positioning. These machines are perfect for medium-scale operations looking to balance efficiency and affordability.
Example: A semi-automatic shrink wrapping machine is ideal for beverage manufacturers packaging bottled juices or water in small batches.
C.Fully Automatic Shrink Wrapping Machines
Fully automatic machines handle the entire process, from loading bottles onto the conveyor to sealing and shrinking the film. They are designed for high-speed production lines and ensure consistent quality.
D.Shrink Tunnel Machines
Shrink tunnel machines work in conjunction with other wrapping systems. They use heat tunnels to shrink film around the bottles evenly, ensuring a professional finish. These machines are essential for large-scale operations.
Key Factors to Consider When Choosing a Shrink Wrapping Machine
Selecting the right shrink wrapping machine involves evaluating various factors, including production needs, product specifications, and operational goals.
A.Production Volume
One of the most critical considerations is the number of bottles your business needs to package daily. For small-scale production, a manual or semi-automatic machine may suffice. However, high-volume operations require fully automatic shrink wrapping machines to handle the demand efficiently.
Example: A large beverage company producing thousands of water bottles daily would benefit from a high-speed automatic shrink wrapping machine to ensure timely and consistent packaging.
B.Bottle Size and Shape
Different machines cater to various bottle sizes and shapes. It’s essential to ensure the machine can accommodate your product dimensions. For instance, a water bottle shrink wrapping machine is specifically designed to handle standard-sized bottles, while others may support customized shapes.
C.Material Compatibility
Shrink wrapping machines are compatible with different types of shrink films. Ensure the machine can handle the type of film you plan to use, as this affects the durability and appearance of the packaging.
D.Speed and Efficiency
For high-speed production lines, the machine’s throughput—measured in bottles per minute (BPM)—is a critical factor. High-speed shrink tunnel machines ensure that large quantities of bottles are wrapped quickly without compromising quality.
Benefits of Shrink Wrapping Machines for Bottles
Shrink wrapping machines offer a range of advantages that make them indispensable in bottle packaging:
A.Enhanced Product Protection
Shrink wrapping provides a secure seal around bottles, protecting them from external damage, dust, and moisture during transportation and storage.
B.Tamper-Evident Packaging
The tight seal acts as a tamper-evident feature, providing consumers with confidence in the product’s safety and authenticity.
C.Improved Aesthetics and Branding
Shrink wrapping creates a sleek and professional look for bottled products. It can also incorporate printed shrink films to display branding, product details, and promotional content.
Example: A bottle shrink wrap machine can create multi-packs with custom branding, enhancing the product’s appeal on retail shelves.
D.Cost-Effective Solutions
By minimizing material waste and labor requirements, shrink wrapping machines provide a cost-effective packaging solution for businesses of all sizes.
Applications of Shrink Wrapping Machines for Bottles
Shrink wrapping machines are used across various industries, each with unique packaging needs.
A.Beverage Industry
In the beverage sector, bottle shrink wrappers are essential for packaging water, soda, and juices. These machines ensure bottles are securely bundled for retail or bulk distribution.
B.Pharmaceutical Industry
Shrink wrapping is critical in pharmaceuticals for securing medicine bottles and providing tamper-evident seals, ensuring consumer safety and regulatory compliance.
C.Food Industry
Shrink wrapping machines are used to package bottled condiments, sauces, and other liquid food items. They help maintain product freshness and prevent leakage.
Integration with Other Packaging Systems
Shrink wrapping machines can be integrated with additional packaging systems to streamline operations and improve efficiency. For example:
- Labeling Machines: Pairing a shrink wrapping machine with an automatic labeling machine ensures bottles are packaged and labeled in a single, continuous process.
- Capping Machines: In beverage and pharmaceutical industries, combining shrink wrapping with capping systems improves the overall production flow.
Maintenance and Support
When investing in shrink wrapping machines, it’s essential to consider maintenance requirements and after-sales support. High-quality machines from reputable manufacturers often come with warranties and readily available spare parts, ensuring minimal downtime.
Tips for Maintenance:
- Regularly inspect the shrink tunnel and sealing components for wear and tear.
- Clean the conveyor system to prevent residue buildup.
- Lubricate moving parts to maintain smooth operation.
Conclusion
Choosing the right shrink wrapping machine for bottles is a strategic decision that can significantly impact your packaging operations. By considering factors such as production volume, bottle size, and speed requirements, businesses can select equipment that aligns with their goals and enhances efficiency.
From semi-automatic shrink wrapping machines for small-scale operations to fully automatic shrink wrapping machines for high-volume production lines, the right choice ensures consistent, professional packaging. Whether it’s the beverage, pharmaceutical, or food industry, shrink wrapping machines deliver secure, tamper-evident, and visually appealing packaging solutions, making them indispensable in today’s competitive market.
Investing in the right shrink wrapping machine ensures your products stand out on the shelves while maintaining the quality and safety that consumers expect.