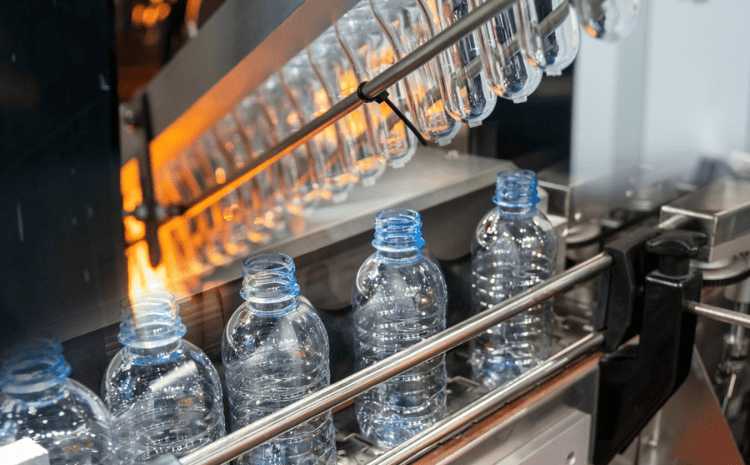
Understanding Shrink Tunnel Packaging Machines for Bottles
In the world of packaging, ensuring that products reach consumers in pristine condition is a priority for manufacturers. Especially in the food and beverage industry, the quality of packaging can influence a product’s appeal, safety, and durability. Among the many types of packaging solutions available, shrink tunnel packaging machines stand out for their efficiency and versatility, particularly in the packaging of bottles. These machines are designed to apply a protective and tamper-evident shrink film around bottles, securing and preserving them for storage, transportation, and display.
Shrink tunnel packaging machines have become a crucial asset for manufacturers aiming to enhance both the functionality and aesthetics of their bottle packaging. In this comprehensive guide, we will explore the importance of shrink tunnel packaging machines, their role in the bottling industry, key features, and how to optimize their performance. Whether you’re involved in packaging for water bottles, carbonated drinks, or any other bottled products, understanding how shrink tunnel packaging machines work can help you improve your production process and maintain a competitive edge.
What is a Shrink Tunnel Packaging Machine?
A shrink tunnel packaging machine is a specialized piece of equipment used to apply shrink film tightly around products, particularly bottles. The machine utilizes heat to shrink the film, conforming it to the shape of the bottle or product being packaged. The result is a secure, tight-fitting seal that provides protection, enhances product presentation, and ensures tamper-evident packaging.
The process begins by loosely applying shrink film to the bottles, which then pass through a heated tunnel. Inside the tunnel, the heat activates the shrinking properties of the film, causing it to contract and tightly wrap around the product. This method is highly efficient and allows manufacturers to package multiple bottles at once, increasing productivity and maintaining uniformity across all packaged products.
Key Components of Shrink Tunnel Packaging Machines
Understanding the key components of a shrink tunnel packaging machine is essential to mastering its operation and optimizing its performance. Below are the primary components that work together to ensure efficient and consistent packaging:
- Conveyor SystemThe conveyor is responsible for moving bottles through the shrink tunnel. It operates at adjustable speeds, allowing manufacturers to control the pace at which products pass through the machine. Depending on the production line’s capacity, conveyors can be designed to handle varying bottle sizes and configurations.
- Heat TunnelThe heat tunnel is the heart of the machine, where the actual shrinking process occurs. This component houses heating elements, usually infrared or electric heaters, which generate controlled, even heat across the film. The heat tunnel can be adjusted in terms of temperature and air circulation to suit the thickness and type of shrink film being used.
- Film DispenserThe film dispenser is responsible for supplying the shrink film, which is wrapped around the bottles before they enter the tunnel. This dispenser feeds the film into the packaging line, ensuring that the correct amount of material is applied to each set of bottles.
- Cooling SectionAfter bottles exit the heat tunnel, they move through the cooling section, where the freshly shrunk film is cooled to maintain its tight fit around the product. This section ensures that the film sets properly and becomes durable enough to protect the bottles during storage and transportation.
- Control PanelThe control panel allows operators to manage the various settings of the machine, including conveyor speed, tunnel temperature, and film feed rate. Modern shrink tunnel packaging machines are often equipped with digital interfaces that offer real-time monitoring, ensuring operators can quickly adjust the machine’s parameters for optimal performance.
Benefits of Shrink Tunnel Packaging Machines for Bottles
The use of shrink tunnel packaging machines in the bottling industry offers numerous benefits, from enhancing product presentation to improving efficiency in the production line. Here are the key advantages of using these machines:
- Product Protection
One of the primary reasons manufacturers use shrink tunnel packaging machines is the protective barrier they provide. The tight-fitting shrink film shields bottles from dust, moisture, and other contaminants, ensuring that products remain in perfect condition throughout transportation and storage. This is particularly important for bottled beverages, where maintaining the product’s freshness and cleanliness is crucial for consumer satisfaction.
- Enhanced Shelf Appeal
In today’s competitive market, the visual appeal of a product is often the first point of contact with consumers. Shrink tunnel packaging helps improve the aesthetic of bottled products by offering a clean, smooth finish that conforms to the shape of the bottle. This enhances the overall brand presentation and can attract more consumers on retail shelves.
- Tamper-Evident Packaging
Security is another critical factor for shrink tunnel packaging machines. The shrink film creates a tamper-evident seal, which provides a clear indication if the product has been tampered with before reaching the consumer. This feature is especially important for bottled beverages and food products, where consumer trust is vital to brand success.
- Versatility in Bottle Types
Shrink tunnel packaging machines are highly versatile and can accommodate a wide range of bottle types, including water bottles, carbonated drink bottles, juice bottles, and more. Whether the bottles are glass, PET, or another material, the shrink film can be adapted to suit different packaging requirements, making the machine suitable for various industries.
- Increased Production Efficiency
The automation provided by shrink tunnel packaging machines streamlines the packaging process, reducing the need for manual labor and increasing production efficiency. The machine can package multiple bottles simultaneously, significantly boosting output and reducing packaging time. This allows manufacturers to meet high production demands without compromising on quality.
- Custom Branding and Labeling
Shrink film can be printed with custom branding and product information, turning the packaging into an effective marketing tool. By incorporating vibrant graphics and detailed product descriptions, manufacturers can enhance their brand’s visibility and engage consumers directly through the packaging.
How Shrink Tunnel Packaging Machines Work for Bottles
To fully understand the efficiency and effectiveness of shrink tunnel packaging machines in the bottling industry, it’s essential to explore the step-by-step process of how these machines operate:
Step 1: Bottle Loading and Film Application
The process begins with the bottles being loaded onto the machine’s conveyor. The film dispenser wraps a thin layer of shrink film around the bottles, which are typically grouped in multi-packs for more efficient packaging.
Step 2: Heat Tunnel Exposure
Once the film is applied, the bottles pass through the heat tunnel. Here, infrared or electric heating elements generate controlled heat, causing the shrink film to contract and conform tightly to the shape of the bottles.
Step 3: Cooling and Setting
After exiting the heat tunnel, the bottles move through the cooling section, where the freshly shrunk film cools down and sets into its final form. This ensures that the film maintains a tight, secure fit around the bottles, protecting them from external elements and keeping the multi-pack configuration intact.
Step 4: Final Product Ejection
The bottles, now securely wrapped, are ejected from the machine and are ready for further processing, such as labeling or direct transportation to distribution centers. The entire process is automated, requiring minimal human intervention and ensuring consistent results.
Types of Shrink Tunnel Packaging Machines
While all shrink tunnel packaging machines operate on the same principle of heat-induced shrinkage, there are different types of machines designed to meet the specific needs of various industries and product types. Here are the main types of shrink tunnel machines used for bottling:
- Standard Heat Shrink Tunnel Machines
These machines are the most commonly used in the bottling industry. They feature a heating tunnel and a cooling section, making them suitable for wrapping bottles of all sizes. They can handle both single bottle applications and multi-pack configurations, such as 6-pack and 12-pack bottle bundles.
- Steam Shrink Tunnel Machines
While less common, steam shrink tunnels are sometimes used when an extra smooth finish is required. These machines use steam to heat the shrink film, creating a flawless appearance without any potential wrinkles or uneven shrinkage. Steam shrink tunnels are often used in the cosmetic or premium beverage industry, where visual appeal is paramount.
- Infrared Shrink Tunnel Machines
Infrared tunnels use specialized infrared heating elements that offer more precise and energy-efficient heating compared to traditional heating methods. These machines are ideal for applications where precise heat control is needed, ensuring even shrinking and preventing damage to sensitive products or materials.
- High-Speed Shrink Tunnel Machines
Designed for high-volume production, high-speed shrink tunnel machines are capable of packaging large quantities of bottles in a short amount of time. These machines are equipped with powerful heating elements and fast conveyor systems, allowing manufacturers to meet high demand without compromising on quality.
Best Practices for Optimizing Shrink Tunnel Packaging Machine Performance
To maximize the performance of shrink tunnel packaging machines and ensure consistent, high-quality results, it’s essential to follow best practices that optimize the machine’s operation. Here are some key strategies for achieving peak performance:
- Optimize Heat Settings
The heat settings in the shrink tunnel play a critical role in the quality of the packaging. Too much heat can cause the film to shrink unevenly or even damage the bottles, while too little heat may result in a loose or ineffective seal. To achieve optimal results, calibrate the tunnel temperature based on the thickness of the shrink film and the type of bottles being packaged.
- Maintain Conveyor Speed
The speed at which bottles pass through the shrink tunnel should be carefully monitored and adjusted based on the type of shrink film being used and the production volume. Faster speeds can reduce packaging time, but if the speed is too high, it may not allow enough time for the film to shrink properly. Balancing conveyor speed with heating time ensures optimal packaging efficiency.
- Regular Maintenance and Cleaning
Regular maintenance is essential to ensure the shrink tunnel packaging machine operates at peak performance. Dust, debris, or film residue can build up in the tunnel or conveyor system, affecting the machine’s efficiency and leading to poor results. Conduct routine inspections, clean the heating elements, and check for any signs of wear and tear on critical components.
- Use High-Quality Shrink Film
The quality of the shrink film used in the packaging process has a significant impact on the final product. Low-quality films may not shrink evenly or could result in weak seals that compromise the integrity of the packaging. Choose high-quality shrink film that is specifically designed for use in shrink tunnel packaging machines to ensure durability, clarity, and consistency.
- Train Operators Effectively
Although shrink tunnel packaging machines are highly automated, it’s still important to have skilled operators who understand how to optimize the machine’s settings. Provide comprehensive training to your staff on how to operate the control panel, adjust heat settings, manage conveyor speed, and troubleshoot common issues. Well-trained operators can quickly identify and address potential problems, ensuring minimal downtime and maintaining high productivity.
Applications of Shrink Tunnel Packaging Machines in the Bottling Industry
Shrink tunnel packaging machines are widely used across different sectors of the bottling industry. Below are some common applications:
- Water Bottles
Water bottles are one of the most widely shrink-wrapped products in the bottling industry. Shrink tunnel packaging machines are used to package multi-packs of water bottles, typically in 6-pack, 12-pack, or even larger configurations, ensuring that they are securely bundled for retail display and transportation. This packaging method helps to protect the bottles from external elements such as dust, moisture, and potential handling damage. The shrink film used in this process creates a clean, professional appearance, which is crucial for consumer appeal, especially in highly competitive retail environments. The transparent or printed shrink film can also feature branding and promotional graphics, enhancing the product’s visibility on store shelves. Additionally, shrink tunnel packaging offers a cost-effective solution for mass production, improving efficiency and reducing the need for secondary packaging materials like cartons or boxes. This method ensures the bottles are securely contained while maintaining the lightweight and streamlined nature of the packaging.
- Carbonated Beverages
For carbonated beverages such as sodas, sparkling water, and energy drinks, shrink tunnel packaging provides an essential solution for maintaining product integrity during transport and storage. The packaging is typically used for multi-packs, where the shrink film ensures that cans or bottles remain securely grouped and protected from shifting or breaking. Carbonated beverages, which are more sensitive to pressure and temperature changes, benefit from the tight seal that shrink wrap provides, as it helps maintain the structural integrity of the bottles or cans. The shrink film also serves as a tamper-evident seal, giving consumers confidence that their purchase has not been tampered with or compromised. Additionally, shrink-wrapped multi-packs are convenient for retail displays, offering a visually appealing presentation. The packaging often features colorful branding and product information, further enhancing the product’s attractiveness on store shelves while protecting the beverages from dust, moisture, and other contaminants.
- Juice Bottles
Juice manufacturers commonly use shrink tunnel packaging to preserve the freshness and integrity of their products. The shrink film used in this process creates a tight, protective seal around juice bottles, safeguarding them from dust, moisture, and external contaminants. This protective layer is crucial in maintaining the quality of juice products, which are often more sensitive to spoilage and contamination compared to other beverages. In addition to offering protection, shrink tunnel packaging enhances the visual appeal of multi-packs with vibrant branding and clear product information printed on the film. This helps juice manufacturers promote their products effectively in the highly competitive beverage market. Whether shrink-wrapping smaller individual bottles or large family-sized juice bottles, the packaging ensures a professional, uniform appearance that appeals to consumers. By providing tamper-evident security, the shrink film also reassures consumers that the product is fresh and safe to drink, boosting brand loyalty.
- Alcoholic Beverages
In the alcoholic beverages sector, shrink tunnel packaging plays a significant role in packaging multi-packs of beer, wine, and spirits. The shrink film offers a secure, protective wrap that prevents bottles from shifting or breaking during handling, transport, or storage. Whether used for glass bottles or aluminum cans, shrink-wrapped packaging ensures the products stay bundled together and are easy to handle by both retailers and consumers. The shrink film also provides tamper-evident protection, ensuring that customers can trust the quality and safety of the product they are purchasing. Additionally, the clear or branded shrink film offers an aesthetically pleasing display for alcoholic beverages, making them more attractive on store shelves. This type of packaging can be customized with brand logos, promotional messages, or seasonal designs, enhancing the product’s marketability. Overall, shrink tunnel packaging provides a cost-effective and efficient way to securely package alcoholic beverages, protecting them while boosting brand visibility.
Future Trends in Shrink Tunnel Packaging Machines
As technology continues to advance, shrink tunnel packaging machines are evolving to become more efficient, flexible, and environmentally friendly. Some of the future trends in the industry include:
- Energy-Efficient Machines
As energy costs continue to rise and sustainability becomes a priority for businesses, manufacturers are increasingly adopting energy-efficient shrink tunnel packaging machines. Newer models are designed with advanced heating systems that optimize energy use, ensuring that the required amount of heat is applied to the shrink film without excessive power consumption. These energy-efficient machines use infrared heaters or other advanced heating technologies, which distribute heat more evenly and reduce energy waste. In addition to reducing operational costs, these machines contribute to a company’s sustainability goals by lowering their overall carbon footprint. By consuming less energy while maintaining high-speed and high-quality production, these machines provide an environmentally responsible solution without sacrificing performance. The shift toward energy-efficient packaging machines aligns with global efforts to reduce industrial energy consumption, making it a key trend in the packaging industry. This focus on energy savings not only benefits the environment but also supports long-term profitability for manufacturers.
- Smart Packaging Solutions
The integration of Internet of Things (IoT) technology is transforming the way packaging machines operate, leading to the rise of smart shrink tunnel machines. These machines are equipped with sensors and data collection systems that allow manufacturers to monitor performance in real-time. By tracking key metrics such as conveyor speed, tunnel temperature, and energy consumption, smart machines provide valuable insights into the production process. Operators can receive alerts if any performance issues arise, enabling them to address potential problems before they impact production efficiency. Furthermore, IoT integration allows for remote monitoring, enabling managers to oversee multiple packaging lines from a central location. This level of automation not only improves operational efficiency but also helps manufacturers make data-driven decisions that can optimize machine performance, reduce downtime, and increase overall productivity. Smart packaging solutions represent the future of packaging technology, offering manufacturers greater control, flexibility, and efficiency in their operations.
- Advanced Shrink Films
The development of advanced shrink films is revolutionizing the packaging industry by offering materials with enhanced properties. These films are designed to provide superior performance in terms of clarity, tear resistance, and shrinking efficiency. For manufacturers, using these new films means better results with fewer defects, reduced material usage, and faster shrinking times. Improved clarity enhances the visual appeal of packaged products, which is especially important in sectors like beverages, where product presentation plays a significant role in consumer purchasing decisions. Tear resistance ensures that the film remains intact during handling, transport, and storage, reducing the risk of damage to the products. Additionally, these films are formulated to shrink more quickly and evenly, which can enhance the overall efficiency of the packaging process. As the demand for cost-effective, durable, and aesthetically pleasing packaging grows, the use of advanced shrink films is becoming increasingly popular, helping manufacturers achieve both functional and marketing objectives.
Conclusion
Shrink tunnel packaging machines play a vital role in the bottling industry, offering numerous benefits, including product protection, enhanced shelf appeal, and tamper-evident security. By automating the packaging process, these machines enable manufacturers to meet high production demands efficiently while ensuring that their products reach consumers in optimal condition.
Understanding how these machines work, their key components, and the best practices for optimizing their performance can help manufacturers maximize productivity and maintain the highest packaging standards. Whether you are packaging water bottles, carbonated drinks, or juice bottles, investing in a shrink tunnel packaging machine will help streamline your packaging operations, improve product presentation, and ultimately drive greater success in the competitive beverage market.