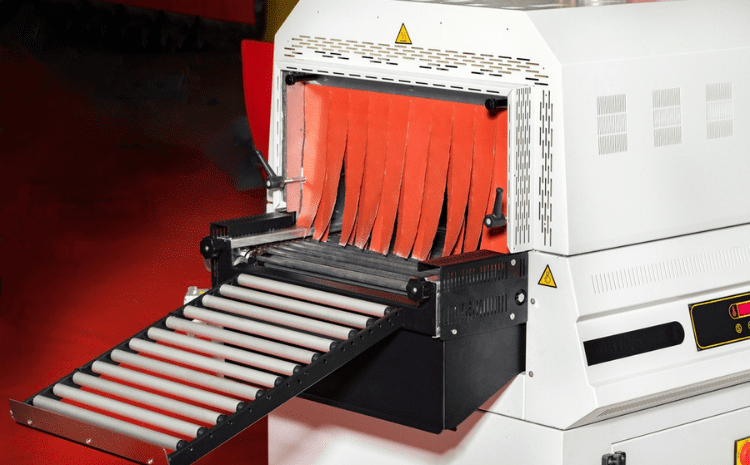
Unveiling the Power of Shrink Tunnel Machines: Streamlining Packaging with Precision
In the dynamic world of packaging, efficiency, reliability, and precision are paramount. Shrink tunnel machines stand as a testament to innovation in the packaging industry, offering a streamlined solution for packaging products with shrink film. These versatile machines utilize heat to shrink film tightly around products, providing a secure and professional packaging finish. In this comprehensive guide, we’ll delve into the evolution, functionalities, benefits, and future trends of shrink tunnel machines, shedding light on their pivotal role in optimizing packaging processes.
Evolution of Shrink Tunnel Machines
The concept of shrink wrapping, which involves applying heat to shrink film around products, originated in the mid-20th century. Initially, shrink wrapping was primarily performed manually or with basic handheld tools, resulting in inconsistent and labor-intensive processes. Recognizing the need for automation, the first shrink tunnel machines emerged in the 1960s, offering improved efficiency and productivity compared to manual methods.
Over the decades, shrink tunnel machines have undergone significant advancements in design, technology, and functionality. From simple conveyorized models to sophisticated high-speed systems, these machines have evolved to meet the diverse needs of various industries. Today, shrink tunnel machines are equipped with advanced features such as digital controls, adjustable temperature settings, and variable speed conveyors, enabling precise and efficient packaging operations.
Functionality of Shrink Tunnel Machines
Shrink tunnel machines are designed to automate the process of applying heat to shrink film around products, creating a secure and professional packaging finish. These machines typically consist of the following components:
- Conveyor System: The conveyor system serves as the transportation mechanism for products through the shrink tunnel. Products are placed on the conveyor belt and transported through the tunnel at a controlled speed.
- Heat Chamber: The heat chamber is the heart of the shrink tunnel machine, where heat is applied to shrink the film around the products. The chamber is equipped with heating elements that generate heat, evenly distributing it to shrink the film uniformly.
- Temperature Control: Modern shrink tunnel machines feature digital temperature control systems that allow operators to adjust the temperature settings based on the type and thickness of the shrink film being used. This ensures optimal shrinkage and prevents overheating or underheating of the film.
- Cooling Zone: After passing through the heat chamber, products enter a cooling zone where the shrink film solidifies and adheres tightly to the products. This cooling process ensures that the shrink-wrapped products maintain their shape and integrity once removed from the machine.
- Variable Speed Control: Some shrink tunnel machines are equipped with variable speed control systems that allow operators to adjust the conveyor speed based on the production requirements. This flexibility enables operators to optimize throughput and ensure consistent shrinkage quality.
Benefits of Shrink Tunnel Machines
The adoption of shrink tunnel machines offers numerous benefits for businesses engaged in packaging operations:
- Increased Efficiency: Shrink tunnel machines automate the packaging process, significantly reducing labor requirements and increasing throughput. By streamlining the shrink-wrapping process, these machines enable businesses to package products more efficiently and meet production targets more effectively.
- Enhanced Product Protection: Shrink film provides a protective barrier around products, safeguarding them against dust, moisture, and tampering during transit and storage. Shrink tunnel machines ensure secure and consistent shrinkage, minimizing the risk of damage or contamination.
- Cost Savings: While the initial investment in shrink tunnel machines may seem significant, the long-term cost savings outweigh the upfront expenses. Reduced labor costs, decreased material wastage, and improved operational efficiency contribute to overall cost efficiency and profitability.
- Versatility and Adaptability: Shrink tunnel machines are highly versatile and can accommodate a wide range of product sizes, shapes, and packaging requirements. Whether shrink-wrapping individual items, multipacks, or irregularly shaped products, these machines can adapt to diverse packaging needs with minimal adjustments.
- Professional Presentation: Shrink-wrapped products have a sleek and professional appearance that enhances their visual appeal on store shelves or during shipping. Shrink tunnel machines ensure uniform shrinkage and tight seals, resulting in attractive and marketable packaging.
Impact on Modern Packaging Operations
The integration of shrink tunnel machines has transformed modern packaging operations in several significant ways:
- Streamlined Workflow: Automated shrink-wrapping processes enable smoother workflow management, allowing businesses to optimize production schedules, reduce bottlenecks, and meet tight deadlines efficiently.
- Productivity and Scalability: Shrink tunnel machines facilitate higher production volumes and accommodate fluctuations in demand without sacrificing packaging quality or efficiency. This scalability is essential for businesses seeking to expand their operations and enter new markets.
- Quality Control and Assurance: Shrink tunnel machines incorporate built-in quality control features such as temperature sensors, conveyor speed monitoring, and seal inspection systems. These systems ensure that shrink-wrapped products meet specified standards consistently, minimizing the risk of defects or rework.
- Customization and Branding Opportunities: With the ability to use custom-printed shrink film and add promotional labels or sleeves, shrink tunnel machines offer opportunities for product customization and branding. Businesses can leverage these capabilities to create unique packaging designs that reinforce brand identity and attract consumer attention.
- Reduced Environmental Impact: Some shrink tunnel machines are designed to use recyclable or biodegradable shrink film materials, minimizing environmental impact and supporting sustainability initiatives. By adopting eco-friendly packaging solutions, businesses can reduce their carbon footprint and appeal to environmentally conscious consumers.
Future Trends and Innovations
Looking ahead, the future of shrink tunnel machines is characterized by ongoing innovation and adaptation to emerging trends. Several key trends are shaping the evolution of these essential packaging machines:
- Integration of Smart Technologies: Shrink tunnel machines will increasingly incorporate smart technologies such as IoT connectivity, predictive maintenance algorithms, and remote monitoring capabilities. These features enable real-time data analysis, proactive maintenance, and enhanced machine performance optimization.
- Automation and Robotics: The integration of robotics into shrink tunnel machines will further automate packaging processes and increase efficiency. Robotic arms and automated handling systems can streamline product loading, positioning, and stacking, minimizing manual labor and maximizing productivity.
- Advanced Control Systems: Future shrink tunnel machines will feature advanced control systems with intuitive interfaces, augmented reality displays, and predictive analytics capabilities. These systems empower operators to monitor and control packaging processes more effectively, leading to improved productivity and quality outcomes.
- Flexible Packaging Solutions: As consumer preferences continue to evolve, shrink tunnel machines will offer greater flexibility in packaging design and customization. From shrink sleeves and multipacks to promotional bundling and seasonal packaging, these machines will adapt to diverse packaging requirements with ease.
- Sustainability and Eco-Friendly Materials: The demand for sustainable packaging solutions will drive the development of shrink tunnel machines that use recyclable, biodegradable, or compostable shrink film materials. These machines will support businesses in their efforts to reduce environmental impact and meet consumer expectations for eco-friendly packaging.
Conclusion
In conclusion, shrink tunnel machines play a crucial role in optimizing packaging processes, providing businesses with a cost-effective and efficient solution for shrink-wrapping products. With their ability to streamline workflow, enhance product protection, and support customization and branding initiatives, these machines are indispensable assets in modern packaging operations.
As we look ahead to the future, shrink tunnel machines will continue to evolve to meet the evolving needs and challenges of the packaging industry. By embracing innovation, sustainability, and customization, these machines will remain at the forefront of packaging technology, driving growth and success for businesses worldwide.