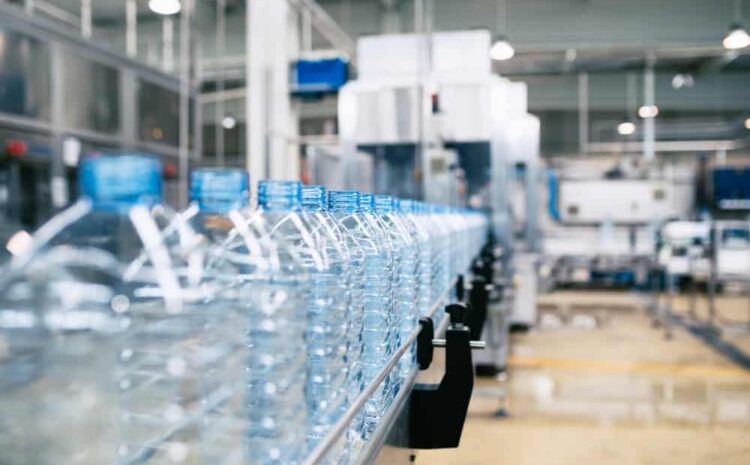
The Rise of Robotics in Industrial Machinery: Enhancing Efficiency and Safety in Manufacturing
In recent years, the world has witnessed a significant shift in the manufacturing landscape, with the incorporation of robotics in industrial machinery playing a pivotal role in this transformation. These cutting-edge systems have redefined the boundaries of efficiency and safety in manufacturing, leading to streamlined production processes and reduced workplace hazards. Robotics in industrial machinery have not only accelerated production timelines but have also minimized human errors, resulting in improved product quality. This article delves into the rise of robotics in industrial machinery, focusing on its profound impact on enhancing efficiency and safety within the manufacturing sector.
The Progression of Robotic Technology in the Manufacturing Sector
The journey of robotics in the manufacturing industry dates back to the early 1960s, when the first industrial robot, Unimate, was introduced to the assembly line. This marked the beginning of a new era in manufacturing automation. Since then, the development and application of robotic technology have progressed at an astounding pace.
Over the years, the scope of robotics has expanded across various sectors, including automotive, electronics, and even plastic bottle filler machines. Technological advancements have enabled robots to perform a diverse range of tasks, from simple pick-and-place operations to complex assembly procedures that require high precision and accuracy.
In the last few decades, the capabilities of industrial robots have evolved significantly, with the introduction of advanced sensors, machine vision systems, and artificial intelligence. These innovations have not only enhanced the efficiency and versatility of robotic systems but also facilitated seamless integration with other industrial machinery and processes.
Today, robots can be found in various forms, from traditional industrial robots with pre-programmed routines to collaborative robots (cobots) designed to work alongside humans in shared workspaces. The progression of robotic technology in manufacturing continues to push the boundaries of efficiency, productivity, and safety, paving the way for a smarter and more automated future.
Enhancing Efficiency with Robotics
A.Increased Production Speed
The integration of robotics in manufacturing has played a significant role in accelerating production processes. Robots, with their ability to operate at high speeds and around the clock, can drastically reduce production times when compared to manual labor. The faster production rates not only lead to increased throughput but also contribute to the timely delivery of products, ultimately resulting in higher customer satisfaction. Furthermore, high speed labeling machines are excellent examples of robotics streamlining packaging and labeling operations, ensuring quicker product dispatch.
B.Enhanced Precision and Accuracy
Robotic systems offer unparalleled levels of accuracy and precision, which greatly impacts the overall quality of manufactured products. Unlike human workers, robots can perform tasks consistently without fatigue or loss of concentration, leading to fewer errors and higher quality output. The reduction of human error in manufacturing processes, especially in tasks that demand high levels of precision, has been one of the most significant benefits of robotics in the industry. This enhanced quality control translates into increased customer satisfaction and a more robust brand reputation.
C.Streamlined Production Lines
The implementation of robotics in production lines has revolutionized the way manufacturing processes are designed and executed. Robots can be seamlessly integrated into existing workflows, often without the need for major infrastructural changes. Their flexibility and adaptability allow for the optimization of production lines, improving overall efficiency and reducing bottlenecks. Moreover, robots can be reprogrammed to perform various tasks, offering greater versatility and making it easier to adapt to changing production needs. The integration of robotics in production lines has ultimately led to leaner and more efficient manufacturing processes, resulting in reduced operating costs and increased competitiveness for businesses.
Improving Safety in Manufacturing through Robotics
A.Hazardous Task Automation
One significant benefit of incorporating robotics into the manufacturing process is the ability to automate hazardous tasks. By employing robots to perform dangerous or repetitive tasks, manufacturers can reduce the risk of workplace accidents and injuries. For example, tasks such as handling hazardous materials, welding, or operating heavy machinery can be delegated to robots, minimizing the potential for human harm. The use of robotics also helps lower the occurrence of repetitive stress injuries among workers. The integration of advanced equipment such as rotary labeling machines further increases the safety of the production environment.
B.Remote Monitoring and Command
The implementation of remote control systems for robotics has greatly enhanced safety in manufacturing settings. These systems enable operators to oversee and manage robotic equipment from a secure distance, minimizing the likelihood of accidents resulting from direct human involvement with machinery. Remote monitoring also enables supervisors to keep a close eye on production processes, ensuring that any potential hazards or deviations from standard procedures are identified and addressed promptly. In addition to improving safety, remote control systems can also contribute to increased productivity, as they allow for quick adjustments and fine-tuning of robotic equipment during operation.
C.Collaborative Robots
The introduction of collaborative robots, or cobots, has marked a significant shift in the manufacturing industry. Unlike traditional industrial robots, cobots are designed to work alongside human workers, complementing their skills and abilities. Cobots are equipped with advanced safety features, such as sensors and force-limiters, that allow them to operate safely in close proximity to humans. This collaboration not only enhances safety but also improves overall efficiency, as cobots can assist in tasks that require human dexterity or decision-making while maintaining a high level of precision and speed. The integration of cobots in manufacturing is a testament to the evolving role of robotics in creating safer and more efficient production environments.
Challenges and Future Prospects
Despite the numerous benefits of incorporating robotics into manufacturing processes, there remain some challenges to overcome. The initial cost of investing in advanced equipment, such as automatic heat shrink machines, can be prohibitive for some manufacturers. Additionally, integrating robotics may require extensive employee training and adjustments to existing workflows. Looking ahead, the future prospects for robotics in manufacturing are promising. Continued advancements in robotics technology, alongside the development of artificial intelligence, are expected to further enhance efficiency, safety, and productivity. As the industry overcomes these challenges, the role of robotics in manufacturing will continue to grow, ultimately revolutionizing the way goods are produced.
In conclusion, the rise of robotics in industrial machinery has brought about significant improvements in manufacturing efficiency and safety. From increased production speed and precision to hazardous task automation and the introduction of collaborative robots, these advancements have transformed the manufacturing landscape. The ongoing innovation and development in robotics technology will continue to push the boundaries of what is possible in the industry, further enhancing productivity while maintaining a safe working environment. As we look to the future, it is crucial to embrace and invest in these technological advancements to reap the benefits they offer in the ever-evolving world of manufacturing.