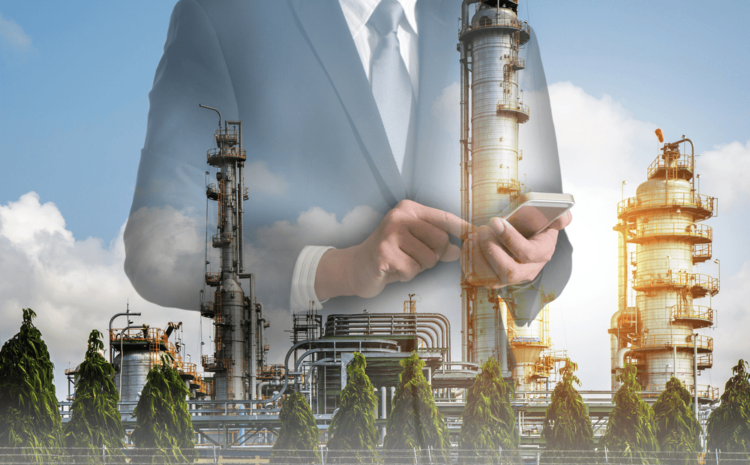
The Future of Blow Molding: Innovations Shaping Tomorrow’s Industry
Blow molding has long been an important part of the industrial industry, changing the production of plastic containers and products. From beverage bottles to automotive components, its versatility and low cost have made aluminum indispensable. As we progress into the twenty-first century, the future of blow molding contains exciting potential, fueled by technology developments, sustainability imperatives, and shifting consumer tastes. In this blog, we’ll look into the important trends and technologies impacting the future of blow molding.
Sustainable Materials:
Every industry has seen a major push toward sustainability in recent years, and blow molding is no different. The use of sustainable materials in blow molding, such as recycled and bioplastic plastics, is key to its future. Bioplastics, which are made from renewable resources like sugarcane or corn starch, present a viable substitute for conventional plastics made from petroleum, lowering reliance on fossil fuels and lessening their environmental effect. Recycled plastics are also used in the blow molding process to minimize energy use and greenhouse gas emissions in addition to keeping garbage out of landfills.
Advanced Manufacturing Technologies:
Future blow molding will be heavily influenced by technology advancements meant to improve productivity, accuracy, and personalization. The way goods are created and made is changing dramatically thanks to advanced manufacturing technologies like additive manufacturing and 3D printing. These technologies give more design flexibility and product differentiation in blow molding by enabling the fabrication of complicated molds with sophisticated geometries. Furthermore, the production process is streamlined by the integration of automation and robotics, which raises productivity and lowers labor costs.
Smart Manufacturing and Industry 4.0:
Industry 4.0 will provide smart manufacturing solutions that use artificial intelligence (AI), Internet of Things (IoT), and data analytics to enhance product quality and streamline production processes. These solutions will define the blow molding industry in the future. In-the-moment maintenance and quality control are made possible by IoT-enabled sensors integrated into blow molding machines, which track and monitor many parameters like temperature, pressure, and cycle duration. Manufacturers can get enhanced efficiency and dependability by utilizing AI algorithms that examine production data to detect trends, adjust parameters, and anticipate any malfunctions.
Customization and Personalization:
As consumer demands shift toward more customized and individualized items, manufacturing processes must become more flexible. Technologies that facilitate mass customization will be adopted in blow molding in the future, enabling producers to create one-of-a-kind, customized items at large quantities. Co-injection molding and in-mold labeling are two examples of techniques that make it easier to integrate colors, textures, and images into molded parts directly, minimizing the need for secondary procedures and lead times. This makes it possible for brands to effectively serve specialized markets and provide a wider range of product possibilities.
Integration of Circular Economy Principles:
Blow molding will eventually adopt more and more of the circular economy’s tenets, seeking to reduce waste and increase resource efficiency all the way through a product’s lifecycle. Manufacturers will optimize product designs to make recycling and disassembly simpler, with a primary focus on design for recyclability. In order to ensure that valuable materials are recovered and repurposed rather than ending up in landfills or the ocean, closed-loop mechanisms will be put in place to collect and recycle used plastic containers.
Molding by Compression Blow:
The principles of injection blow molding and extrusion blow molding are combined in compression blow molding. In the same way as extrusion blow molding, it starts with the extrusion of a parison. Still, the parison is first inserted into a mold cavity rather than being directly blasted with air. Subsequently, the mold shuts, and the parison is expanded to fit the mold’s shape using compressed air.Better control over the distribution of wall thickness and superior neck finish quality are provided by compression blow molding. Large, asymmetrically formed containers like car fuel tanks are frequently made with it.
Blow molding with injection stretch (ISBM):
PET (polyethylene terephthalate) bottles are mainly made using a two-stage technique called injection stretch blow molding. Initially, an injection-molded preform with a thick bottom and a threaded neck is used. After that, the preform is reheated and given its final shape by being stretched longitudinally and blasted into a mold cavity.The use of ISBM enables the creation of robust, lightweight containers and provides exact control over bottle dimensions. Pharmacies, beverages, and cosmetics are among the things it is frequently used for packaging.
Blow molding, a versatile plastic manufacturing process, encompasses various subtypes, each with unique advantages and applications. Here, we’ve explored additional techniques beyond the commonly known extrusion, injection, and stretch blow molding. Compression blow molding, for instance, merges features of extrusion and injection blow molding, offering superior control over container wall thickness and neck finish quality. This makes it ideal for producing large, irregularly shaped containers like automotive fuel tanks. Injection stretch blow molding (ISBM) stands out for its precision in crafting PET bottles. With ISBM, manufacturers can achieve precise control over bottle dimensions and create lightweight yet durable containers suitable for beverages, cosmetics, and pharmaceuticals. Continuous extrusion blow molding presents a continuous manufacturing process, ensuring high-volume production of consistent, dimensionally accurate containers. Its efficiency and productivity make it a preferred choice for small to medium-sized containers. Incorporating these advanced blow molding techniques into manufacturing processes opens up new possibilities for industries ranging from packaging and automotive to healthcare and consumer goods. As technology continues to evolve, so too will the capabilities and applications of blow molding, shaping the future of plastic manufacturing.
Blow molding has a bright and exciting future full of potential thanks to advancements in technology, growing consumer demands, and environmental requirements. The blow molding sector is well-positioned to prosper in the coming years by embracing sustainable materials, cutting-edge manufacturing technology, intelligent manufacturing solutions, customized capabilities, and circular economy concepts. The future of blow molding has the promise of an inventive, efficient, and sustainable business as manufacturers embrace the opportunity these developments present.